この問題は製品外観を決める上で設計者にとって非常に大切な事です。
射出成形における製品取り出しの仕組みで勉強頂いたように、
基本的に凹形状がコア側に来るように金型設計を行います。成形サイクルでは金型が開いた時には樹脂冷却に伴ってコア側に食らいついた製品がエジェクターでつき出されて、取り出し機に回収されていくのが理想です。
この時、コア側にはエジェクターピンのピン跡がつきます。
キャビ側には樹脂が流れ込むゲート(これはサイドゲートやトンネルゲートにすることで側面に動かすことは可能)が発生します。
でも製品の外観面にピン跡がつくのはどうしても嫌だ!
こうおっしゃられるお客様は多数いらっしゃいます。お気持ちも察します。そんなエジェクターピンによる突き出しが製品形状上NGな場合はプレート突き出しを応用する事が出来ます。
プレート突きだしとは
通常エジェクターピンで製品を突き出す所を、プレートで代用することによって製品を突き出す方法。製品面にピン跡が残らず、製品の取り出しも安定します。
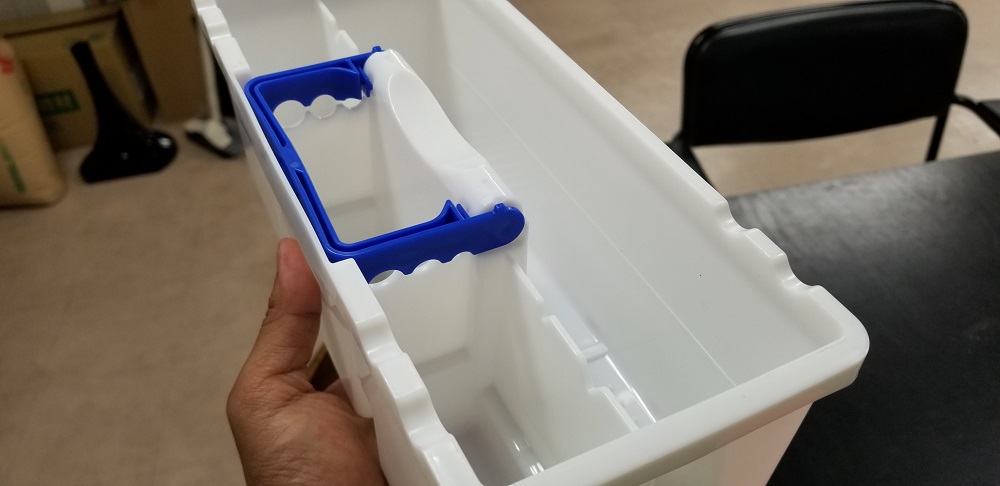
↑この製品は画材用のバケツですが、天面がコア側になっています。水を入れる部分がどうしても金型上、凸形状になるのでコア側になります。ここではピン跡を残さない様、天面をエジェクタープレートで突き出しています。
製品形状や選定樹脂により、ガス逃げが悪い事が想定される場合はプレートをいくつかに分散したブロック突き出しがありますが、金型技術とより多くの工程が要求されるため金型費用が高くつく傾向があります。
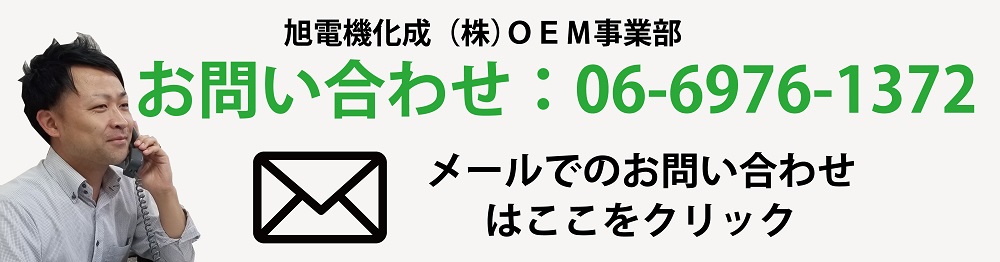